Six tips on how to effectively reduce CNC machining costs
Six tips on how to effectively reduce CNC machining costs
In order to make the parts have better cutting processing structure manufacturability in CNC machining, the following principles should be considered in the structural design, the longer the time required for CNC to process the parts, the higher the cost. Stemming from this rule are many other factors, such as material selection (materials that are easier to machine are faster and therefore less expensive to use) and part design, how part design affects and reduces CNC machining costs.
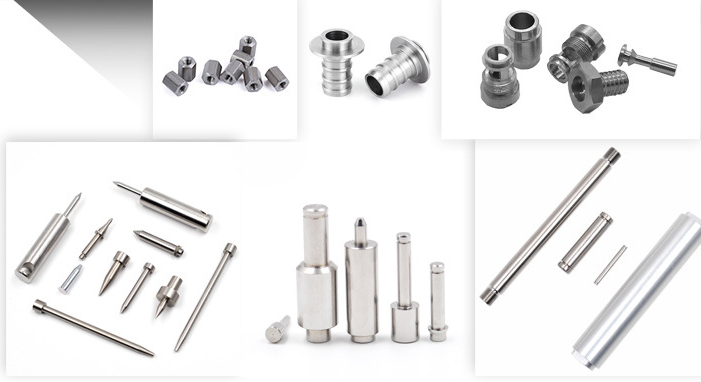
1. Avoid thin walls
Although CNC machining is capable of producing parts with extremely tight tolerances and thin walls (about 1 mm), it is recommended to be as thick-walled as possible if cost is the driving factor for your product. The reason for this is because machining very thin walls can be tricky: if done too quickly, parts can be damaged by vibration. Correctly machining thin walls requires repeating low cutting depths, which significantly increases the time of the machining process. Therefore, integrating thicker walls as much as possible into the part can help speed up machining time and reduce costs.
2. Radius within the points
When designing parts, integrating an internal radius instead of a 90-degree angle at a corner will save a lot of machining time (and cost!). )。 Because CNC milling tools are cylindrical in nature, they naturally have curves or radii when they create corners within a part. Keeping this in mind, designing parts with internal radii instead of sharp corners can simplify the production process. In addition, the larger the inner radius, the larger the milling cutter that can be used and the faster the machining time.
3. Avoid deep cavities
Another design tip that helps minimize CNC machining costs is to avoid deep cavities and grooves in the part. The reasons for this are twofold. First of all, the deeper the cavity, the longer it will take to cut the material. Secondly, designing parts with cavities larger than 4 times the diameter of the tool may require specialized tooling and increase production costs.
4. Avoid deep threads
Following on from the previous tip, it is also recommended to keep the thread depth as low as possible to reduce machining costs. Unless absolutely critical to a given part, it is usually not necessary to integrate threads with a depth greater than three times the diameter of the hole. Deeper threads, such as deep cavities, may require the use of non-standard tools, which can increase machining time and cost.
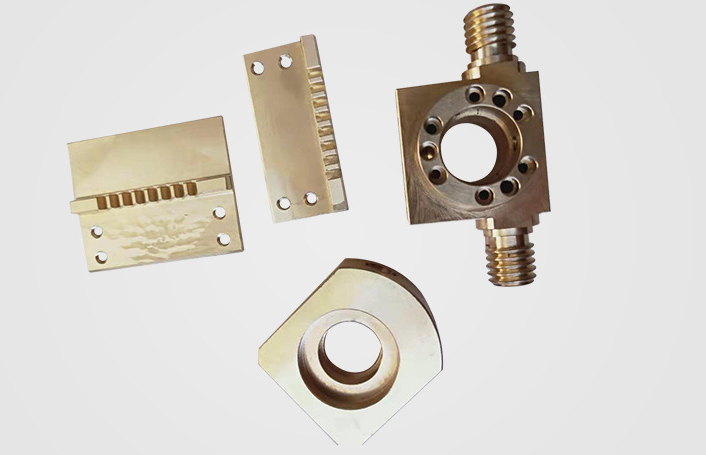
5. Stick to standard tool sizes
When designing parts, significant machining time can be saved by ensuring that the dimensions corresponding to standard CNC tools are maintained. For example, hole, thread and cavity diameters should correspond to commonly used CNC tool diameters. In addition, by maintaining the same hole and cavity size on the part, fewer tool changes are required, speeding up the CNC machining process.
6. Avoid high tolerances
Although CNC machining is able to withstand some of the highest tolerances in any manufacturing process, that doesn't mean every part needs the tightest tolerances. In fact, using tight tolerances only when absolutely necessary can significantly reduce costs, as achieving high tolerances increases machining time (and therefore inspection time).
Bolusi Group is a Chinese CNC machining manufacturer engaged in the design and production of CNC hardware, hardware shell and precision parts. Focus on CNC machining of hardware, CNC machining of aluminum parts, CNC machining of aluminum alloy and other products, and provide all kinds of hardware
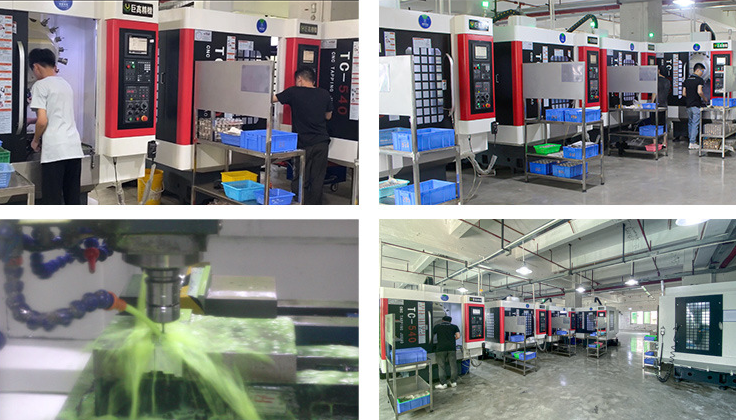
Bolusi Group is a Chinese CNC machining manufacturer engaged in the design and production of CNC hardware, hardware shell and precision parts. Focus on CNC machining of hardware, CNC machining of aluminum parts, CNC machining of aluminum alloy and other products, and provide all kinds of hardware
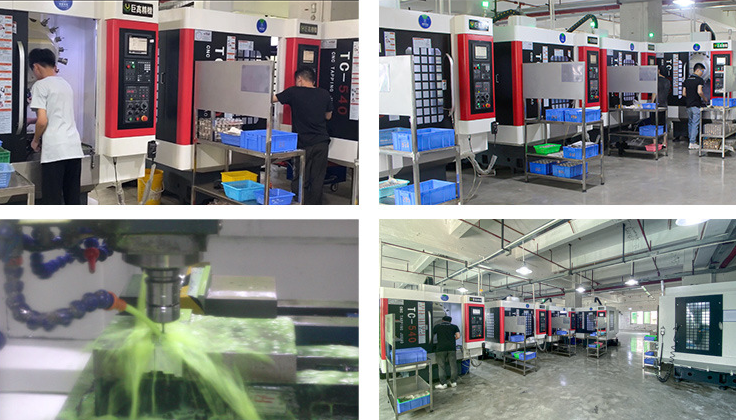
Latest News
Contact Us
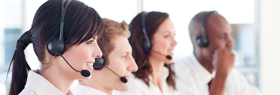
Name: Mike
Tel: +8613662873457
E-mail: sales@bolusigroup.com
Whatsapp: +8613662873457
Add: No.10 Sanjiang Industrial Zone,Hengli Town,Dongguan City,Guangdong Provice,China